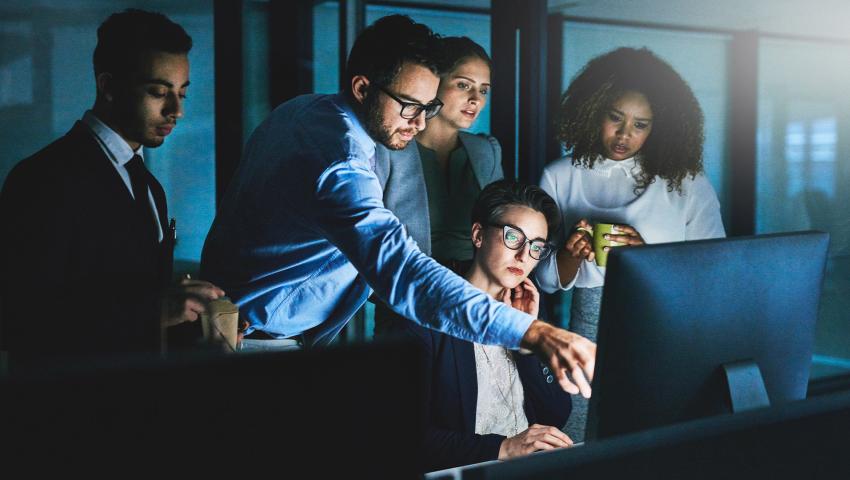
Operation Management
Operations Management consulting focuses on helping businesses streamline their operations, improve efficiency, reduce costs, and ensure high-quality outputs. This service aims to optimize the processes, resources, and technologies involved in the production and delivery of products or services.
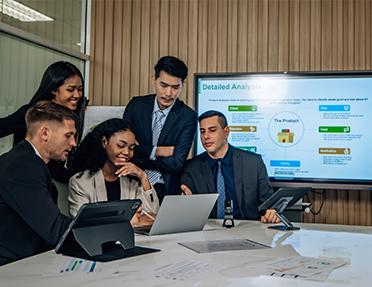
Benefits of Operations Management Consulting:
- Improved Efficiency
- Cost Reduction
- Enhanced Quality Control
- Increased Flexibility
- Risk Mitigation
- Better Resource Utilization
- Faster Time-to-Market
- Sustainability & Compliance
- Technology Adoption
- Scalability
Key Components of Operations Management:
- Process Optimization
- Objective: Improve operational efficiency by analyzing and refining business processes to reduce waste, lower costs, and enhance productivity.
- Activities: Process mapping, bottleneck identification, process re-engineering, and automation to create lean and efficient workflows.
- Supply Chain Management
- Objective: Enhance the flow of goods and services from suppliers to customers, ensuring timely delivery and cost efficiency.
- Activities: Supply chain analysis, inventory management, vendor relationship management, demand forecasting, and logistics optimization.
- Lean & Six Sigma Implementation
- Objective: Apply Lean and Six Sigma methodologies to eliminate waste, reduce variability, and improve quality across operations.
- Activities: Process standardization, root cause analysis, continuous improvement initiatives, and implementing Lean/Six Sigma principles to drive performance excellence.
- Quality Management Systems (QMS)
- Objective: Establish systems and processes to ensure that products or services meet or exceed quality standards.
- Activities: Implementing ISO standards, setting up quality control and quality assurance systems, and conducting regular audits to monitor performance and compliance.
- Production Planning & Control
- Objective: Ensure that production processes are efficient and aligned with demand, avoiding overproduction or delays.
- Activities: Capacity planning, scheduling, resource allocation, and monitoring production flow to meet delivery timelines and customer requirements.
- Inventory Management
- Objective: Optimize inventory levels to balance customer demand with cost-efficiency, minimizing excess stock while avoiding shortages.
- Activities: Implementing inventory control systems, using just-in-time (JIT) practices, and integrating technology like Enterprise Resource Planning (ERP) for real-time tracking.
- Operations Risk Management
- Objective: Identify and mitigate risks that could disrupt operations, from supply chain interruptions to production downtime.
- Activities: Conducting risk assessments, implementing contingency plans, and ensuring business continuity through disaster recovery strategies.
- Technology & Automation Integration
- Objective: Leverage technology to automate repetitive tasks, improve efficiency, and reduce errors in operations.
- Activities: Assessing current technology infrastructure, recommending automation tools (e.g., robotic process automation, AI, IoT), and integrating these technologies into operations.
- Sustainability in Operations
- Objective: Implement environmentally sustainable practices in operations, reducing waste, energy consumption, and carbon footprint.
- Activities: Introducing eco-friendly production processes, waste reduction strategies, and energy-efficient technologies to align with sustainability goals.
- Cost Efficiency & Resource Optimization
- Objective: Achieve cost reductions by improving the efficient use of resources, such as labor, materials, and equipment.
- Activities: Conducting cost-benefit analysis, optimizing resource allocation, and implementing cost-saving measures across production and logistics.